Home > Products & Services > Repair and Field Services > Preventive / Predictive Maintenance Programs
Preventive / Predictive Maintenance Programs
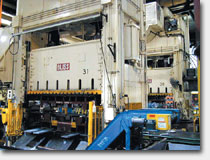
Montezum Bliss Press
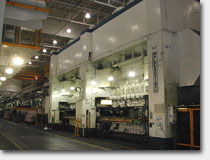
Preventive Predictive Maintenance
Midwest Brake will develop and manage a preventive maintenance program tailored to your needs. A proper preventive maintenance program will provide for regular inspections to evaluate your equipment's current condition. A report will be generated to document current conditions of your machine and will be used as a basis for recommending repairs and identify areas of wear for scheduling future repairs.
- Services
- Develop implement and manage a preventive maintenance program tailored to your needs.
- Perform preventive maintenance to your equipment.
- Track changes to equipment and make recommendations.
- Start up inspection
- Use data collected to develop a predictive maintenance program to reduce downtime and eliminate unplanned failures.
A key element in implementing a successful preventive maintenance program is planning and scheduling. By scheduling regular inspections to obtain machine data and record this information, proper analysis can be performed and this can be used to reduce downtime and eliminate unplanned failures.
- What Should A Good PM Program Include
- Machine cleaning and general housekeeping.
- Daily operator inspections.
- Lubrication
- Periodic Inspections
- Non-destructive testing. (Thermography, vibration analysis, ultra-Sonics, spectrographic oil analysis etc.)
- Maintenance to correct deficiencies found through non-destructive testing and inspections.
- Minor adjustments
- Pre-planned repairs
- Machine rebuilds
- PM plan is designed by machine.
- 80% of all PM's to be accomplished with machine running.
- PM plan should be condition driven. (Machine condition deteriorates with hours of operation. PM's have to be adjusted accordingly.)
- Requirements for Building a PM Program for Presses
- Perform a FMEA.
- Complete press inspection.
- Analyze machine history if available.
- Determine mean time to failures. (on common failures)
- Operator input.
- Review scheduled run time. Hrs. /day, days/week.
- Construct and write PM's (using photos to illustrate.)
- Present and review PM's on site.
- Schedule and implement plan
- Training. (this would include building a process for recording and tracking all data gathered)
- Benefits
- Reduction in unplanned downtime which increases machine efficiency.
- 40 - 60% reduction in downtime in approx. 2 yrs.
- More effective utilization of manpower.
- Reduced manpower requirements.
- Improved product quality.
- Increased capacity. (typically 15 - 40% after 1 to 3 years)
- Decreased maintenance costs (typically 30% over time)
- Increased OEE.
- Safer work environment.
- Keys to Implementing a Successful PM Plan
- Management support
- Competent, responsible craftsmen and operators who take ownership of the process.
- Scheduling
- Execution
- Monitor the process.
- PM task should include a list of tools, equipment and parts necessary to perform the task.
- All manual lube points should be clearly marked.
- Photographs for reference attached to the task documentation.